Building
a 4" Rotary Table
Suitable for the Taig Mill
Part Three
The next step is to make the worm gear mounting ring and bore out the
gear.
The worm gear I got was pre bored for 1/4", and had a hub extension of
about 1/2".
The gear must go over the .750" shaft on the table hub, and it will
have nothing left
for mounting it by the time it is bored for that diameter.
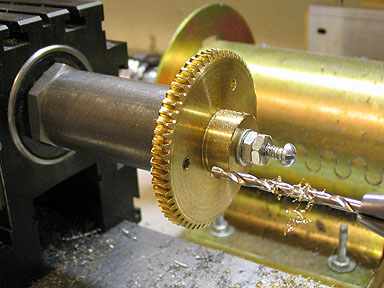
On the left is the gear mounting ring, and on the right, the
gear. The ring is 1.5" in diameter,
and is made from CRS. A 1/4" hole is drilled in the center, to
match that in the gear. For
work holding, a Taig arbor has a 1/4" dia. shoulder turned on the end
so the ring will be held
on the center line of the spindle, and three holes are spotted on a
1.25" hole pattern. The same
hole pattern is drilled into the gear, using the same Taig arbor.
The holes in the gear are then drilled out to pass 4-40 screws, and the
holes in the ring are drilled and
tapped for 4-40 threads. You can see my goof on the ring. I
had started to spot the holes
without tightening up the arbor on the spindle. By the time I got
to the third hole, I realized something
was wrong. I marked the bad hole marks with a marker, and after
tightening the arbor, started the
hole pattern again in a different position.
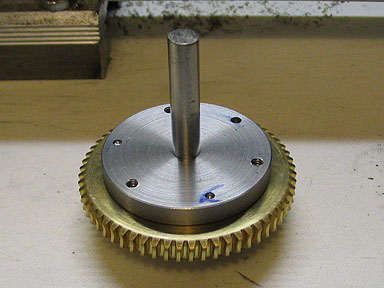
Once the holes are done, a piece of 1/4" drill rod is used to align the
gear and it's ring, and the
three screws are tightened down to hold the two pieces together for
boring. Then the drill rod
piece is removed from the hole.
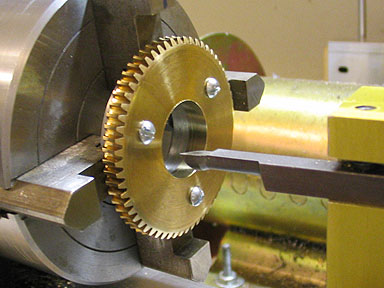
The two pieces are then indicated in with the four jaw chuck.
Note that the chuck is not bearing
on the gear teeth, but holding the ring, behind it. The pieces
need to be indicated both on the
diameter or the ring, and the face of the gear.
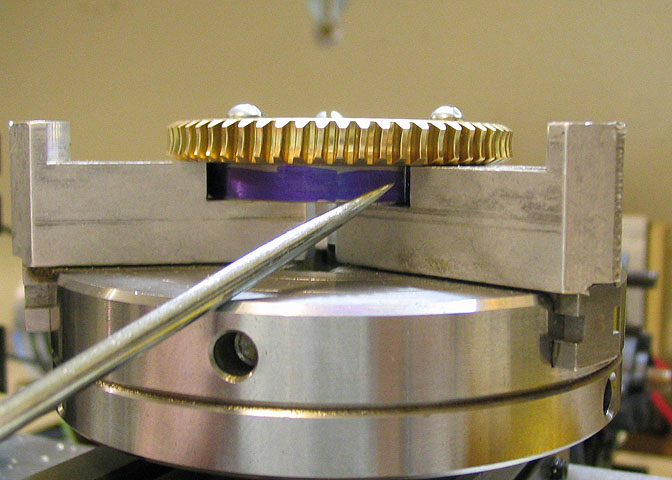
Once the bore for the gear and ring is finished, the assembly goes into
the three jaw chuck
for marking out another hole pattern. The holes that go into the
edge of the ring are tapped for
6-32 set screws. To save having to tap the entire depth of the
hole, half the depth of the hole
can be drilled out to clear the set screw, with just the bottom half
being tapped.

A shot of the finished set screw holes in the gear mounting ring.
You can see the other
two holes inside the bore of the ring.

Everything is assembled at this point to help find the location of the
set screw flats that need
to be milled in the table hub.
The hub and table are bolted together and laid face down on the
bench. Then the base is set on
on the table and the bearing is slipped over the hub shaft and aligned
in the race, which will
align the parts. The gear and it's mounting are put on the hub
shaft, and the jam nut is finally
cinched down to pre load the bearing. It just needs to be
tightened down a little. Then use an
Allen wrench to tighten the three set screws onto the hub shaft.
They are only tightened a little.
Just enough to make a small mark in the hub shaft.
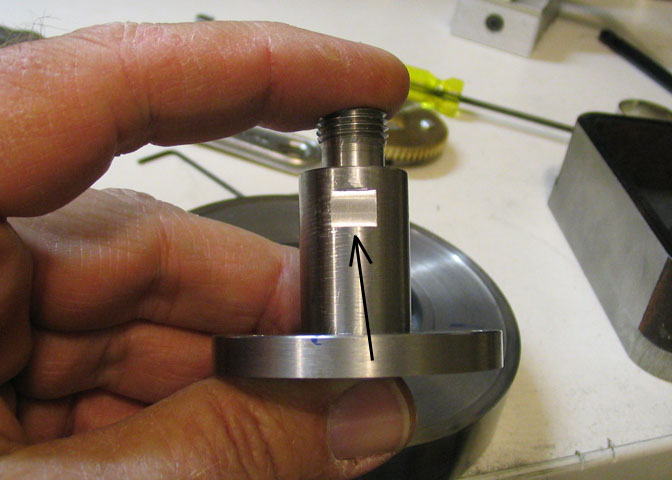
Then the whole thing is disassembled and three flats are milled at the
location of the marks
made by the set screws. If this isn't done, and the set screws
are tightened down hard on the
shaft without the flats, you won't be able to remove the
bearing. The set screws will raise a
bur that will not allow the bearing to pass.
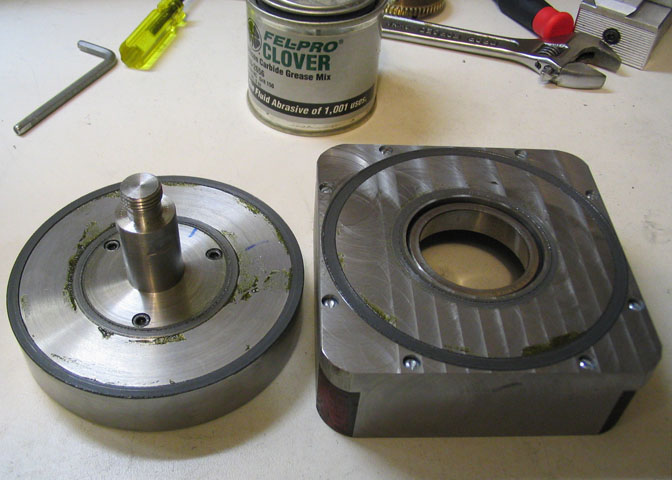
The hub is replaced in its' recess in the table top, and the running
surfaces of the table
and base are lapped in. Everything must be reassembled for this
step, but the set screws
for the gear ring are not tightened. Clover Compound is used for
lapping. I used 150 grit.
The Clover is spread in a light coat on the running surface of the
table top, the whole thing
is assembled, and the table is turned 'round and 'round on the
base. Turn it five or ten rotations,
tighten the jam nut a little, and turn some more. When it
feels smooth through its' 360 degree
rotation, it's done. This took only about five minutes.
Care must be taken not to get the Clover in the bearing. It
will ruin it and the race in short order.
When the lapping is finished, everything is disassembled, and all parts
are cleaned very, (very)
well. There is always the possibility that some of the Clover
will get into the bearing. The bad
news is that it will have to be replaced. The good news is
they're cheap. Less than $15.
When everything is nice and clean again, the bearing is oiled, and the
whole shebang
is assembled again in preparation for the next step. On assembly,
the bearing is pre-
loaded just enough to hold the table top to the base snugly, but not so
much that the
table can't be rotated.
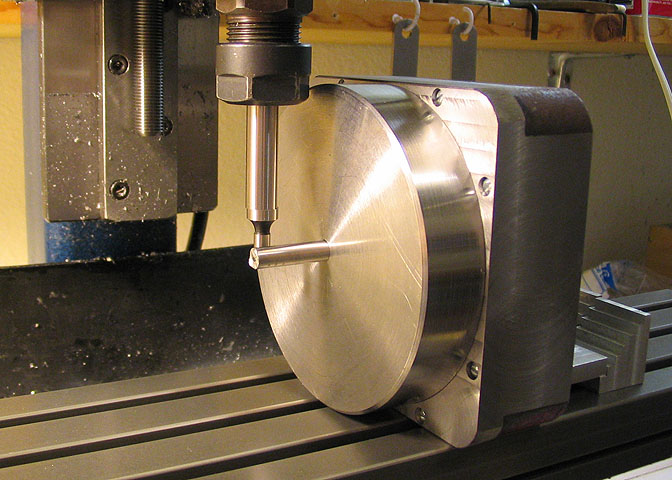
Remember the hole that was reamed in the table top, way back at the
beginning? Time to use it.
The table assembly is now mounted nice and square to the mill table,
and a piece of 1/4" drill rod
is inserted into the hole in the table top. This is used as a
reference for finding the center of the
table hub. The edge of the drill rod is found with an edge
finder, and the mill table is dialed over
to put the center line of the table/hub/shaft assembly under the mill
spindle. Then the spindle is
raised, and the Y axis is cranked to the left so the second co-ordinate
can be located off the face
of the gear.
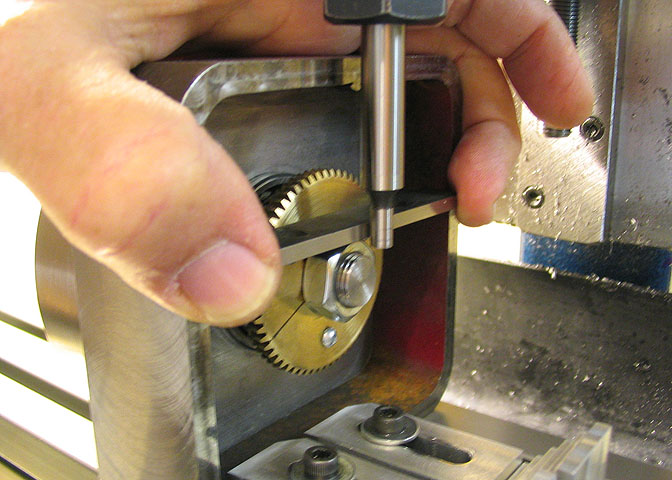
To find the edge of the outer side of the gear a .500" parallel is held
against the gear surface, and
the edge finder is used again for a location. Then the pieces are
added up, and the Y axis is
cranked back for that amount; The gear is .219" thick. The
edge finder pin is .200" in diameter.
Add half the gear thickness, (call it .110"), to half the diameter of
the edge finder pin, (.100"), and
the width of the parallel, (.500"), and the Y axis dial in is
found: .110" + .100" + .500" = .710".
Dial that in and the spindle will be directly over the center line and
in the middle of the gear face.
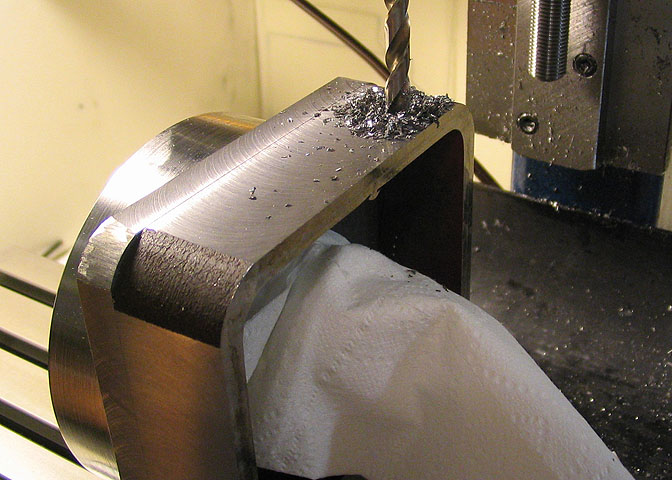
The last co-ordinate to dial in it the set-over for the worm gear
shaft. The diametral pitch of the gear
is 1.875" and the D.P. of the worm is .438". Add those two
together and divide by two to get 1.1565",
or, to make it a little easier on the eyes, say 1.157". The
backlash is taken up on the X axis, and
that amount is dialed in. An extra thou or two wouldn't have
hurt. It's a really close fit, as it is.
The first hole is spotted and drilled 15/64" through the top surface.
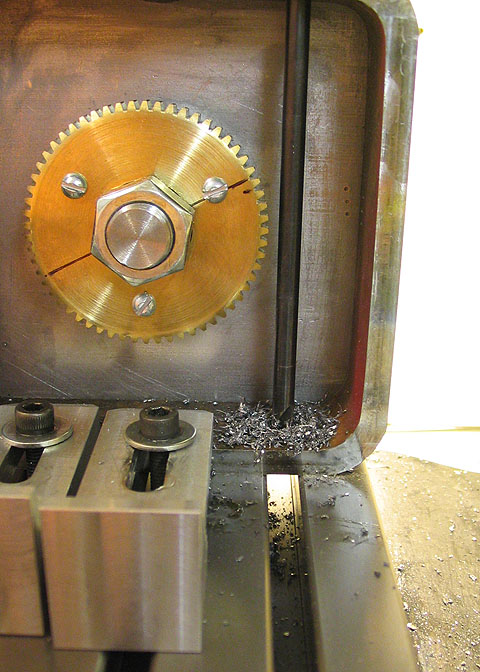
The bottom hole is drilled using an extra long 15/64" bit. This
hole has to be started with a
light touch on the Z axis feed so the drill doesn't wander all
over. I just got lucky in the shot
above. The location of the hole was centered perfectly over one
of the T-slots in the mill table.
The plan was to drill half way through this bottom part, then transfer
the piece to the drill
press to finish the hole. As it was, after this hole was drilled,
a 1/4" reamer was run through
both holes on one pass, and for the moment, this operation is
done. I'll return to it later.
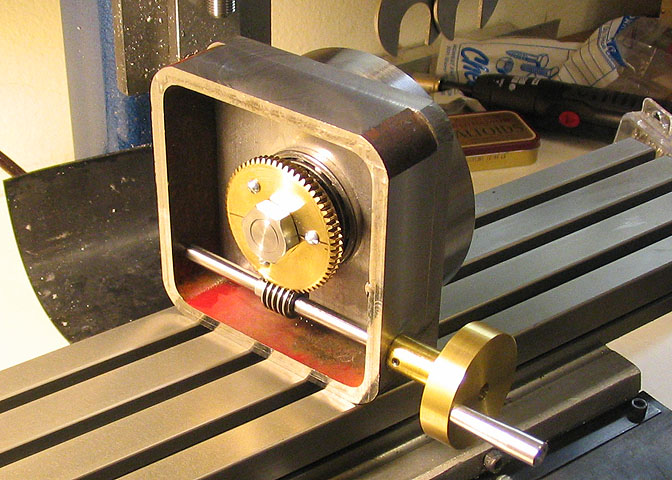
A piece of drill rod and a spare handle are used to check the fit of
the worm to the gear. This is
not the handle that will be used for the finished piece.
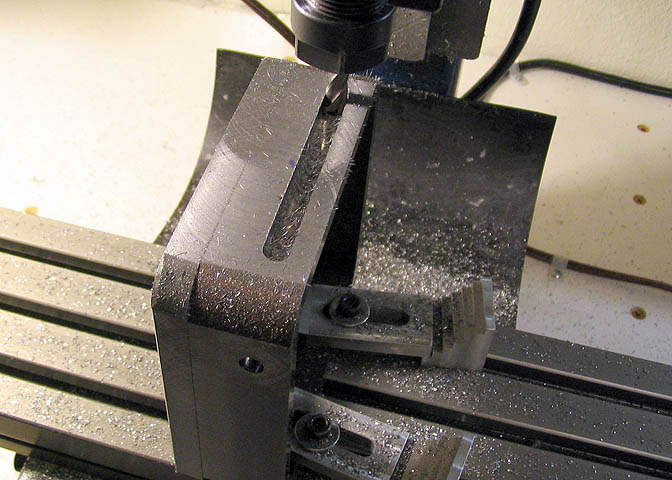
Again, the table is disassembled, and the base mounted on the mill to
cut the hold down slots, or pockets.
One slot on the right, one on the left. The two sides with the
holes for the worm shaft do not get the slots.
The slot is .270" wide and the bottom edge is 1/4" from the bottom edge
of the base. It starts 5/8" from
the front edge and ends 5/8" from the back edge. (The front edge
is the one with the hole drilled in it
in this picture.)

While the table top is off the base, the clamping groove can be
turned. The compound slide is used
to get a cut off tool into position for the cut, since the piece is too
large to swing over the cross slide.
The groove to be cut starts .125" from the bottom of the table top and
is .150" wide and .125" deep.
This takes a while since light cuts must be taken on such a large
piece. The brown piece of paper
under the compound provides some friction between the compound and the
cross slide to help keep
the compound in place. Without it, the compound has a tendency to
slip on the cross slide, since it
is hanging off the front of the cross slide, and the clamp for it is
not terribly strong.
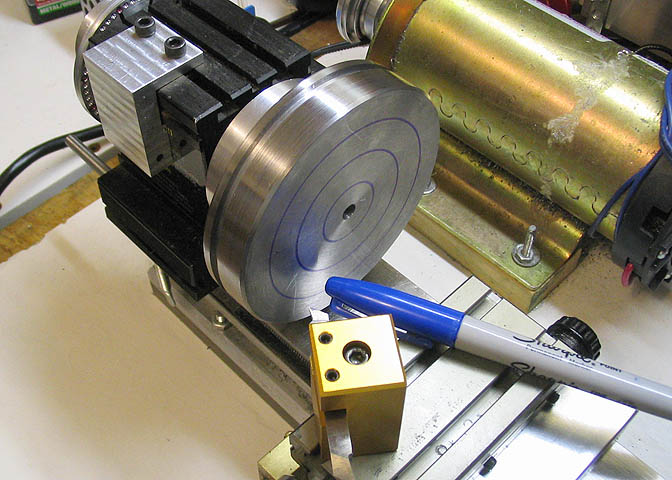
The finished clamping groove can be seen in this shot.
I've used a Sharpie marker to check out the positions of the alignment
rings on the top of the
table. They are one, two, and three inches in diameter, and are
cut .015" deep and .025" wide.
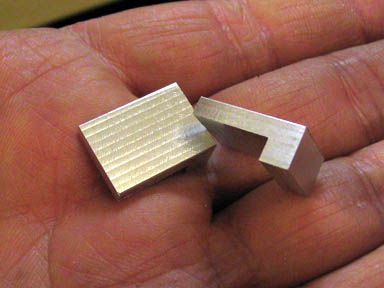
The next thing on the list are the two hold down clamps that will lock
the table.
These pieces have to be made before the next operation on the table top.
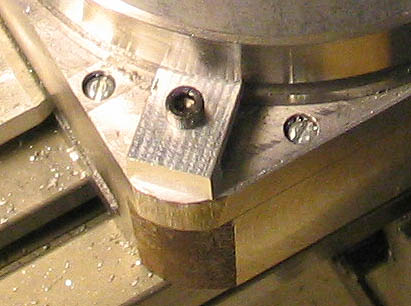
When the clamps have been milled out they are drilled to pass a 6-32
screw,
and the top of the base is drilled and tapped for same directly beneath
the clamp.
Click on the link to page four.
Part Four
Part
One
Part
Two
Part
Five
Note:
Stephen
Campbell followed my progress on this table as it was being
built.
I work from a simple sketch, and am
not so good using a CAD drawing
program,
so Steve very kindly made the drawings
going by my measurements.
Long story
short, if there should be any errors
in the drawings, they are MY
fault, not Steve's.
A heartfelt Thank
You
to Steve for all his good work!
The drawing is in a PDF file, so you need Acrobat to open it, (still
free, I understand).
Rotary
Table Drawings
More Taig Lathe & Mill Projects
deansphotographica.com
(home page)
Copyright Dean Williams