Building
a Small Screwless Vise
Part Three
(Part
One is Here)
(Part Two is here)
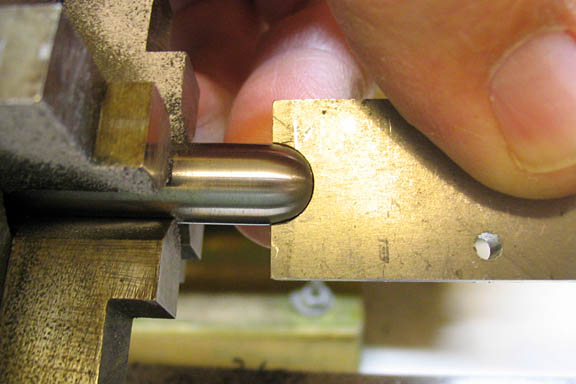
A cutter needs to be made to cut the button recess in the top of the
moveable jaw.
W-1 drill rod, 3/8" dia is used. A radius is cut on the end
to form half a sphere. A
radius cutter would be nice, but that's a project pretty far down on my
list, so I just cut
a large chamfer on the end of the drill rod, and then used a gage and a
file to finish it.
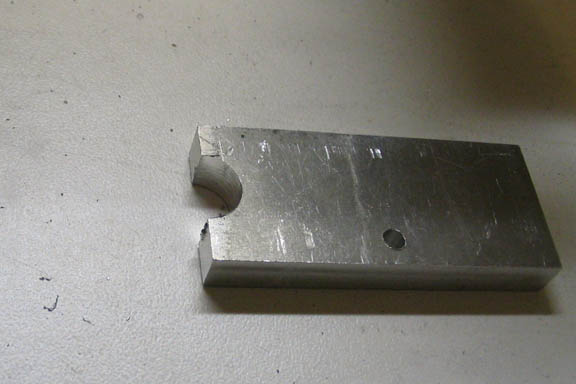
The gage can be easily made by milling out half the diameter with a
3/8" end mill. If a
gage is needed that can't be made with a standard sized end mill, the
proper sized
drill bit can be used. Drill a hole in your gage plate, and mill
half of it away.
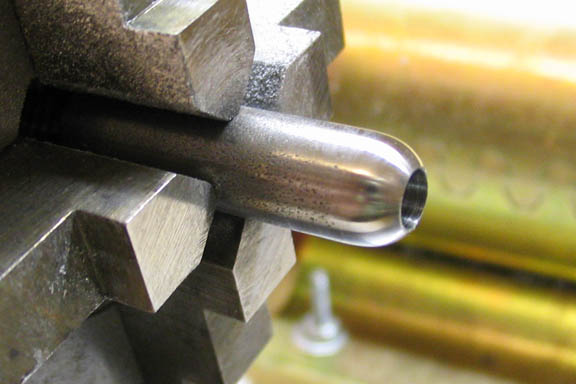
While I'm at the lathe, might as well make the pivot button, too.
Another piece of 3/8"
rod is chucked up, faced off, and before cutting the radius on the end,
a spot is drilled
with a center drill. The radius is then turned, and a clearance
hole for a 10-32 screw is
drilled, 1/2" deep.
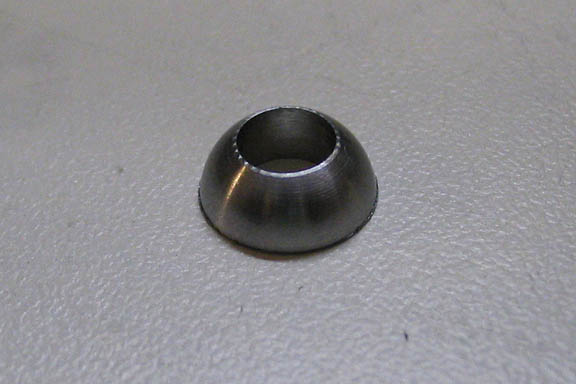
Then the button is parted off just behind the radius.
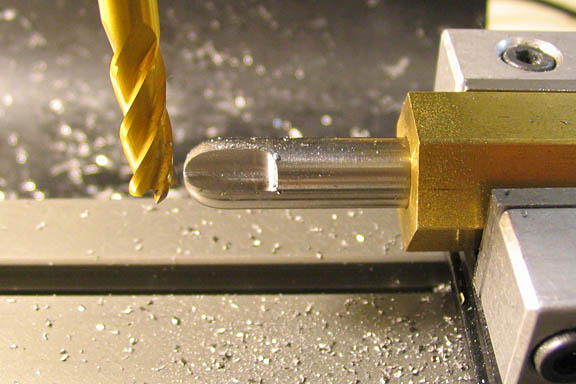
Back to the cutter now, a piece of hex rod is used for a positioning
fixture. The hex
rod is bored for a running fit with the drill rod and a set screw hole
is drilled and tapped.
The cutter is milled, rotating the hex rod two flats after milling each
cutting edge.

After milling, a Dremel tool is used to grind a small relief behind
each cutting
edge. It would be better to make a jig for grinding the relief,
but since this is
probably the only time I will use this cutter, the hand grinder will
work fine. You
just have to be careful to keep the grinding disc behind the cutting
edge of the cutter.
The blued area is the face of the cutting edge. I blued it so I
wouldn't grind the
relief on the wrong side of the cutting edge. Rotation of the
mill spindle needs
to be taken into account when preparing cutters.
After honing the face of the cutting edges, the cutter is hardened and
tempered,
then honed again as necessary.
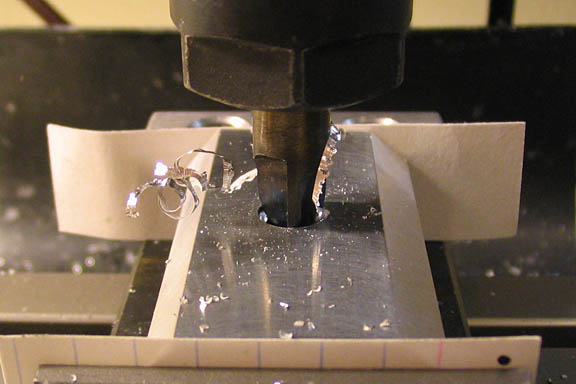
The movable jaw is put back into the vise and located via the counter
bored hole
that was milled in an earlier step. The existing #10 clearance
hole is drilled out to
1/4" and then the button pivot cutter is mounted in the mill
spindle. The cutter has
a very flat face on the cutting edges, so it is run at the lowest
spindle speed and advanced
a little at a time, checking often until the button fits nicely
in the pivot hole.
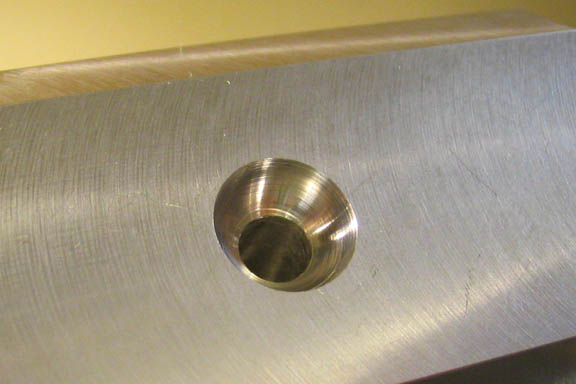
The finished button pivot hole.
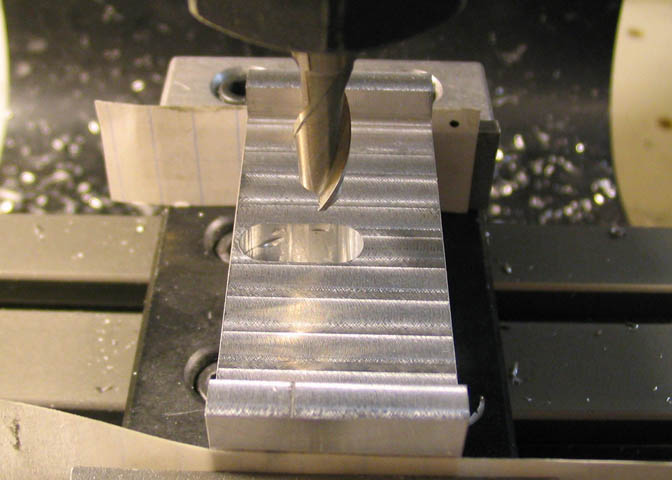
Now a pocket is milled in the bottom of the moveable jaw to allow the
screw to
pivot when tightening down the jaw. The pocket is milled right up
to the edge of
the clamping side of the jaw, and toward the back of the jaw just until
the end mill
comes to the back side of the pivot hole, being careful not to cut
through the jaw.
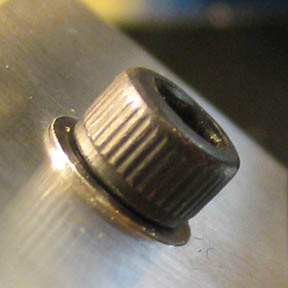
These shots illustrate how the pivot button moves as the jaw tightened.
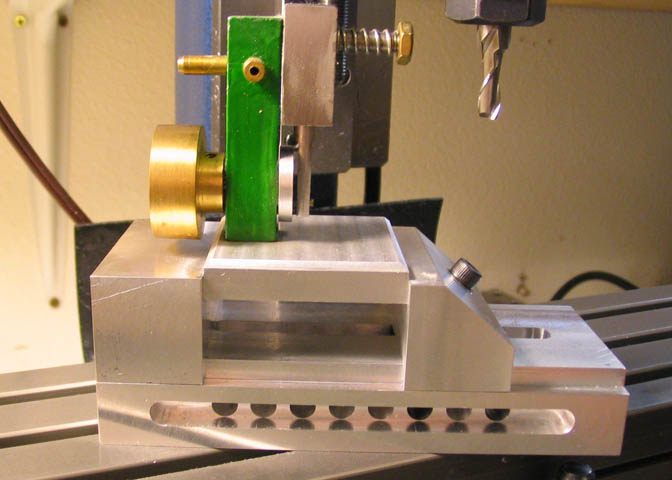
So there it is, actually clamping something! It's 2.25" wide and
will take
a 3" work piece
if used as it is. It will get brass jaw liners when time permits.
Thanks for having a look.
A few sketches follow. All units are in inches. Click on
one to go to a larger size.
These don't represent proper drafting conventions or practices.
They are just sketches
with some dimensions. For clarity, not all aspects of each piece
is included in each view,
but there should be enough here for most folks.
Someone might notice that on the third drawing, the radius called out
for on the pivot button
is .188", when the diameter of the button is noted as .375".
Obviously, the radius should
read .1875". If you want to use the sketches as a guide, look
them over well. Everyone
makes mistakes, and you may find some here.
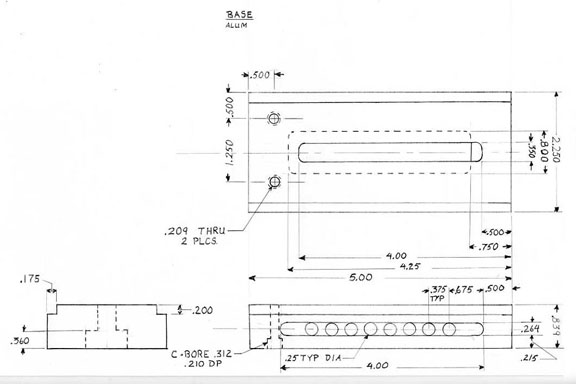
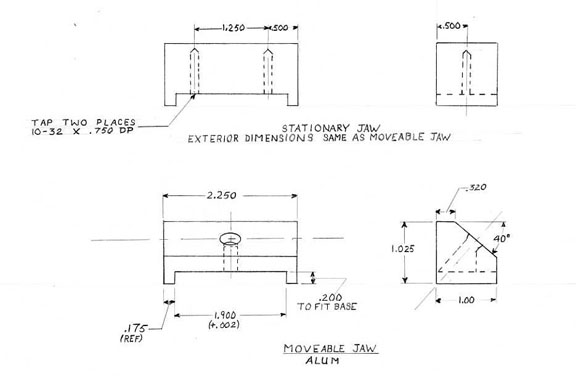
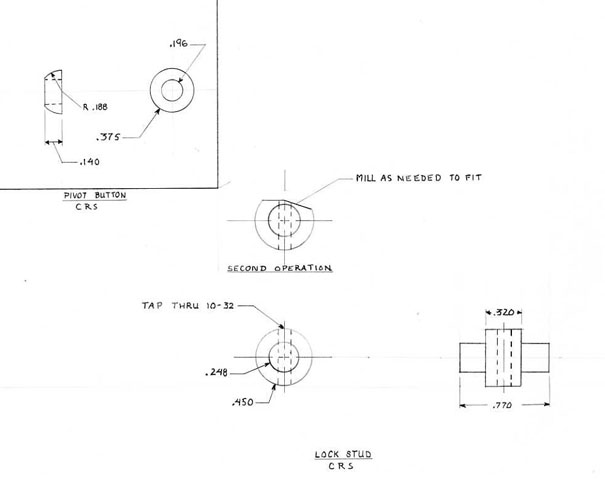
A nice fellow named Steve Campbell sent me a CAD drawing he made of the
vise.
It's a PDF file, so should open if you have Adobe Reader. Thanks
much, Steve!
CAD
Vise drawing by Steve Campbell.
Go
back to Part Two
Go back to Part One
More Taig Lathe & Mill Projects
deansphotographica.com
(home page)
Copyright 2009 Dean Williams