Atlas 618 Spindle Removal
This article deals with the older Atlas 618 models with bronze
sleeve bearings.
Removing the spindle from one of these machines is not especially
tricky, but needs
to be done properly to prevent damage to some pretty expensive parts.
It may come in handy for someone needing new bearings, but the same
procedure, (minus the
bearing replacement) has to be done if you simply need to replace the
drive belt on the lathe,
or if you need to replace the thrust bearing, or step pulley bushings.
Sleeve bearings for these lathes can still be had from Clausing, and
from parts houses
that carry standard sintered bronze bearings. They are a standard
size.
In case you would like to order from Clausing, the PN's
are L9-14 for the large front one
and L2-14 for the smaller rear one.
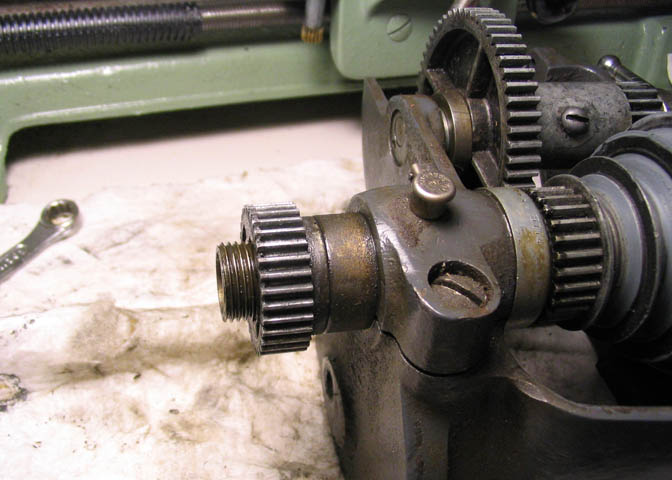
To start with, pull the power
cord for the lathe.
Remove the lock collar on the back end of the spindle. In the
shot above, it's already been
removed. It has a single set screw in it, so back it off a turn,
and remove the collar. The collar
is round, and has no flats or anything to put a wrench on. I'm
not going to tell you to put pliers on
it to remove it.. Go your own way on that. Some primate had
used a hard hammer on the back
end of this spindle in the past, so the collar was hard to
remove. It is a right hand thread.
There is a soft BB in the bottom of the hole for the set screw so the
screw doesn't bur the threads
on the end of the spindle. Don't loose it.
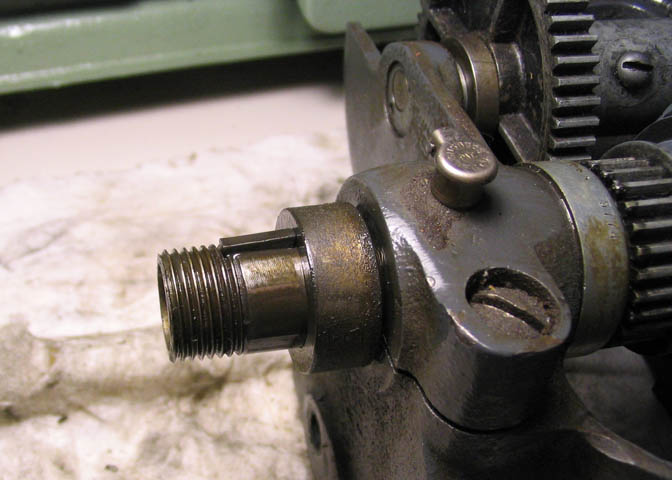
Then pull off the main spindle gear, and remove the Woodruff key.
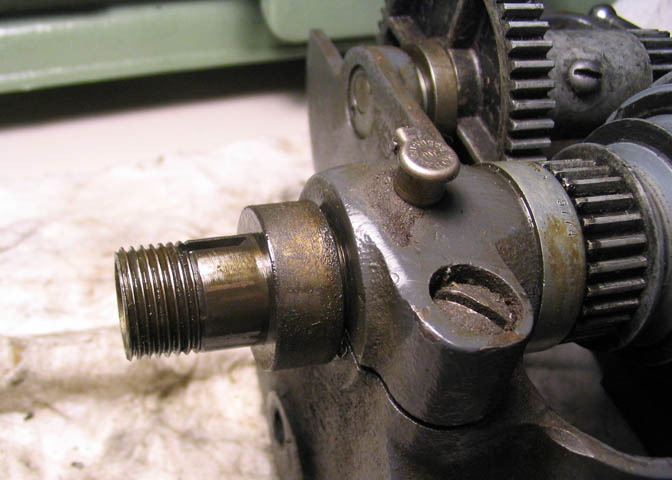
After that, you can pull off this thrust collar.
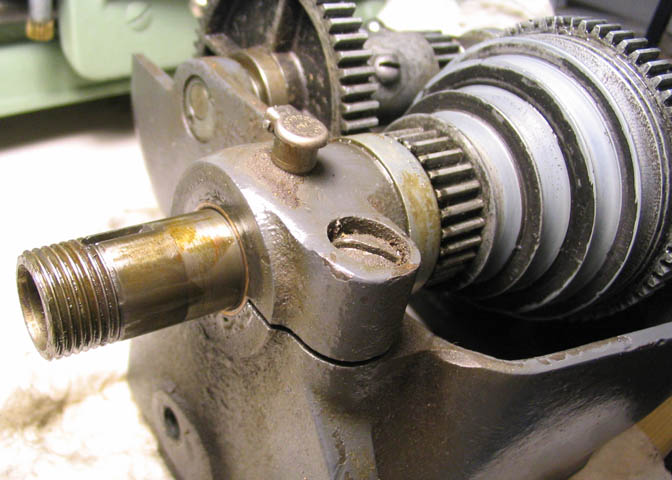
It should look like this when you have the pieces on the back end
removed.
Now would be a good time to slack off the two big screws in the bearing
caps. You can see one of them
in the picture above, and there is one on the chuck end of the spindle,
too. Back them off until they are
loose, then just barely snug them down. The idea is to get the
spindle out without the bearings
following it at the same time.
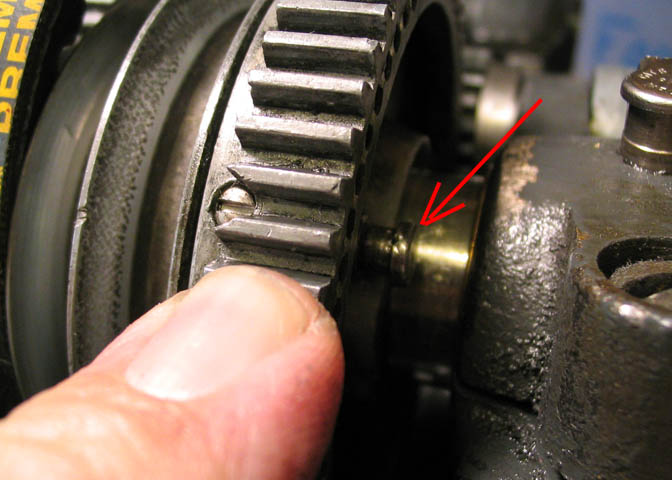
Now, get a look at the bull gear lock pin. There is a screw at
the edge of the bull gear in this shot.
That is for oil. Rotate the bull gear 180 degrees, and you will
see another hole opposite the oil hole shown here.
(You don't need to take out the oil screw shown in the picture above.)
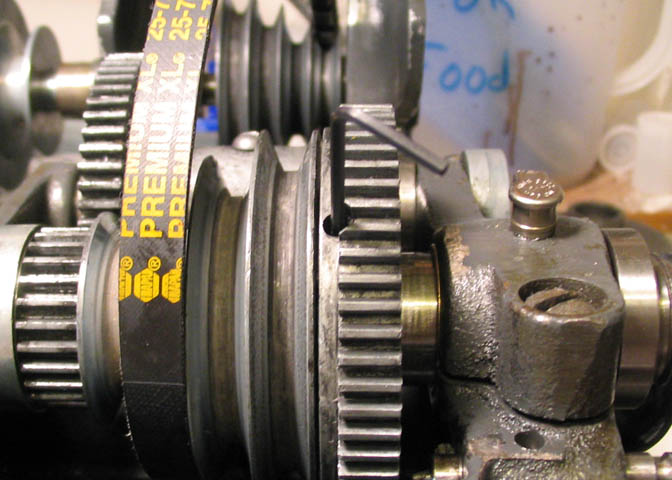
When you find the second bull gear hole, reach way down to the bottom
of it with a 5/64" allen
wrench and loosen the set screw a couple of turns. That set screw
is only there to keep the bull
gear from sliding along the spindle, but has to be loose to get the
spindle out.
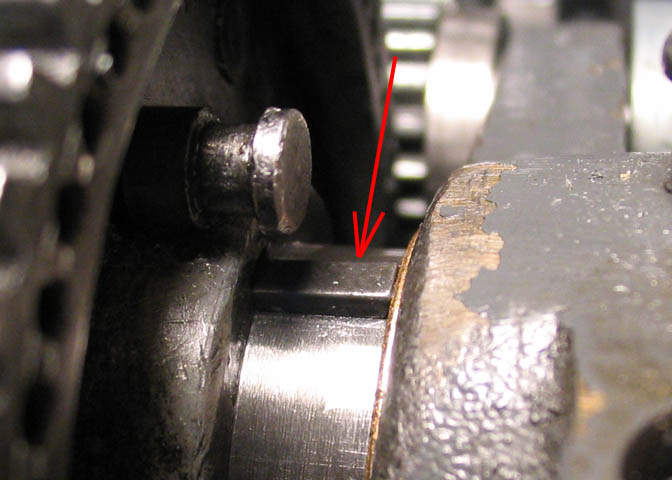
Now, unless there are other problems, (I'll save that for later), you
should be able to slide the
spindle toward the tail stock. At this point, you only want to
pull it out of the nose end of the
head stock about 3/8", until you can see the Woodruff key, as in the
picture above.
Take that key out, but don't pull the spindle any farther toward the
tail stock end of the lathe yet!
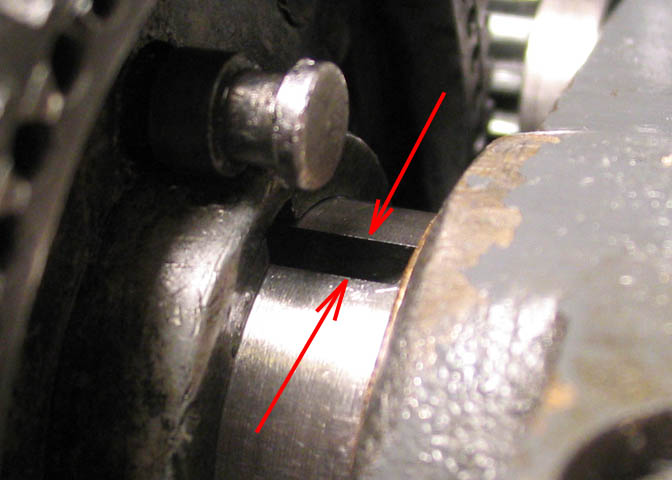
When the key is out, check very carefully at the corners and ends of
the Woodruff keyway. Use
a fine file to gently remove any burs that you see. Then gently
turn the spindle 180 degrees and
look for the place where the set screw in the bull gear pinched on the
spindle shaft. File that spot
down too. These two places do not run in the spindle bearings, so
filing them won't hurt anything
in that respect. The bull gear sits over the top of both of these
spots, and is always in the same
relationship to them, so there is no danger of the filing job doing any
harm to it, either.
If you should just yard the spindle out of the head stock without doing
the above, and there are
burs at these points, you'll score the bearings. I'm replacing
the bearings right now, but what if I just
needed a belt? You have to take the spindle out to get a new belt
on too. You don't want to ruin your
bearings just to replace a belt, so check these two points carefully.
Once those burs are dressed down, reach in with a tissue and clean off
any filings, and then you
can pull the spindle out slowly.
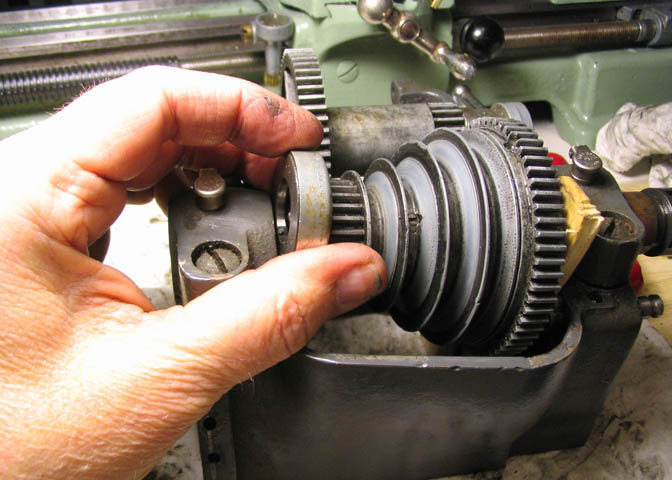
As you pull the spindle out, catch the thrust bearing. At about
this point, the spindle diameter
will change at the nose end of the head stock. It gets smaller,
so don't let the spindle
drop onto the bearing.
Note the small screw in the second pulley groove. That is for
oil. Nothing else. It lubes the step
pulley bushings. (It's supposed to be oiled each day that you
will use the back gear.)
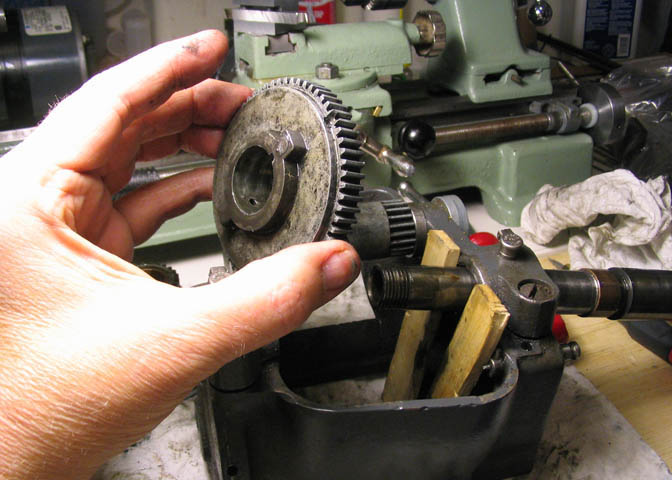
Keep pulling the spindle out, first grabbing the step pulley, then the
bull gear,
so they don't fall down into the head stock cavity
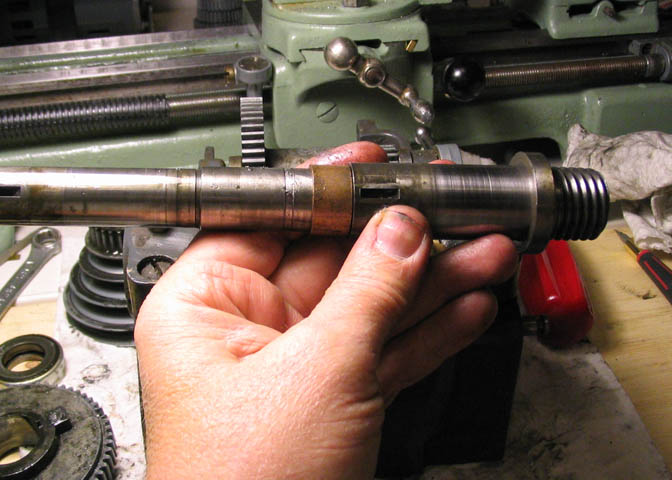
Now, I actually did have trouble with this one. The bushing you
see on the spindle in the
shot above is supposed to stay in the step pulley. I had to tap
the spindle out with a piece of
wood because the small bushing was stuck on the spindle.
There are two of those bushings, and they should both be pressed into
the step pulley. They
allow the pulley to spin on the spindle independent of the bull gear
when you have the back
gear engaged.
I soaked this for a while in solvent, and the bushing came off pretty
easy.
I pressed it back into the step pulley, and all is well.
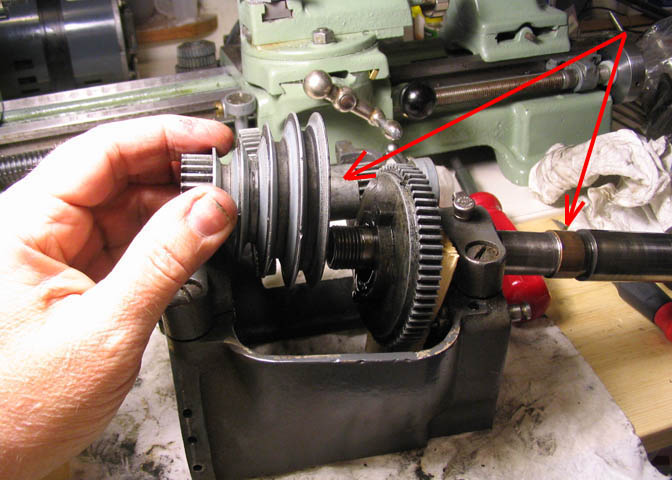
In this shot you can see what I'm talking about.
That bushing on the spindle was supposed to stay in the pulley.
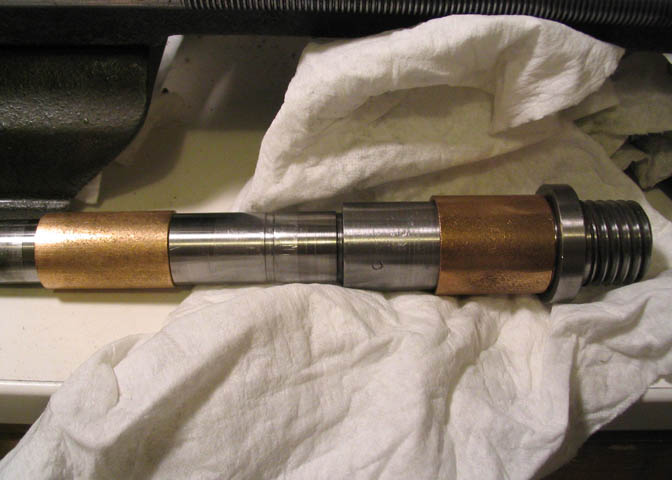
With the spindle nice and clean, I tried the new sleeve bearings to
make sure they were the right
size, before I take out the old bearings.
In this picture, the tiny circle near the larger bearing is where the
bull gear set screw has raised a
mark that I was talking about earlier, and this is one of the things
that had to be filed down before
pulling the spindle through the bearings.
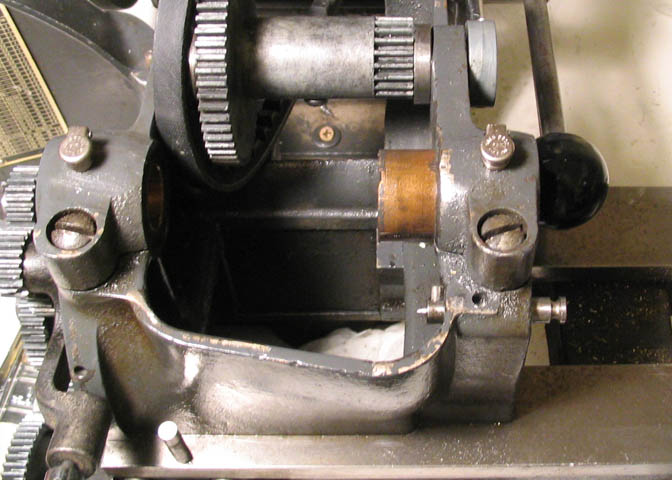
To get the old bearings out, make sure the bearing cap screws are
loose, and use a piece of
wood or plastic to tap them toward the inside of the head stock.
Both the front (big) and rear
(small) bearings would move a little by hard pressure with my thumb,
but I couldn't press far
enough into the hole to get them all the way out. So, tap, tap,
with something soft.
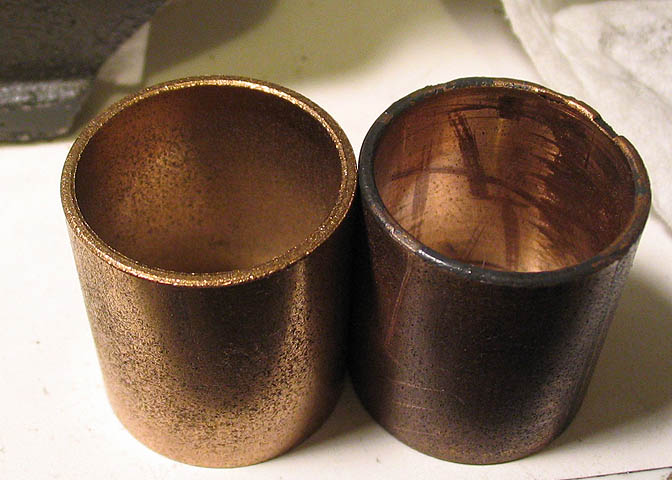
Guess which one is the old bearing? :)
The old one, (ok, on the right!) still has factory paint on it, so it's
been in there a long time. You
can see that it's taken a beating a few times too, by the marks left
from someone whacking on the
end of the spindle without removing the Woodruff key.
I expect it's 50-60 years old. Reading on lathes/uk, it says
there were no more plain bearing lathes
after around 1957-59, if I recall. So, it's done it's job for a
long time.
There are some straight marks in there that are no doubt from previous
spindle removal, but there
is also a rather large spot of radial scuffing on the far right, which
looks similar to what you see
sometimes in crank bearing shells in car engines. Many miles.
Putting the new bearings back in is just a matter of cleaning out the
head stock, oiling the outside of
the bearings, and pushing them back in. If they seem a little
tight, make sure the bearing cap screw
are loose first, then try again. If they are still tight, try
this;
Screw down the bearing cap screws until you feel them just barely start
to get tight. I'm talking about
the point where you feel them touch the top of the hole as they thread
in, where if you screwed them
in any further, they would start to squeeze the bearing caps.
(Don't screw them down hard. You'll
break the caps.) Then back out the screw just a touch, so it is
free, like 1/20 of a turn. Use a thin
wedge of wood, and tap it into the parting line of the bearing cap to
spread them just a thou or two.
Be careful. Don't hit the head stock casting with anything
metal. Use a tiny plastic headed hammer
to tap in the wedge, and then just a little bit. This will spread
the cap enough to let you get the bearing
started in the bore straight. Then you should be able to put a
small piece of wood on the end of the bearing
and push it in with the palm of your hand. I had to bump it
in with the ball of my palm to get the big one
in all the way. The small one went easier. Then pull the
wedge(s) out and again, make sure the
cap screws are loose.
Oil up the spindle with light oil, and put it back in the head stock to
see that it fits without any of
the other gears/pulleys and other things. It should spin
freely. Take it back out and start putting
all the parts on it as you feed it through the bearings, taking care
not to knock it on the bearings as
you do so. Don't forget the Woodruff key that goes in the bull
gear.
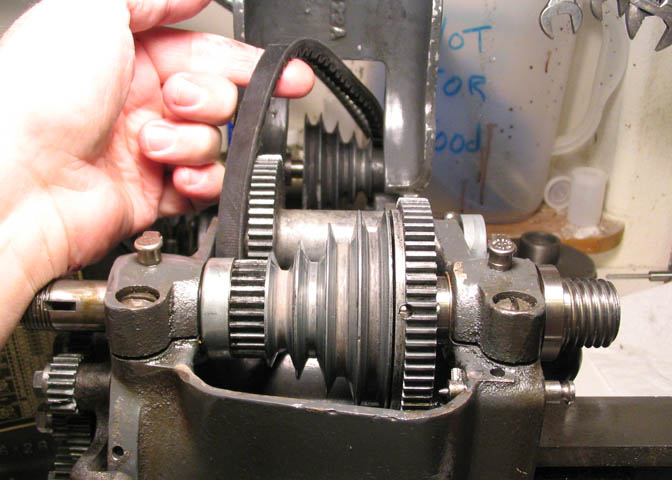
After you get it put back in, if you are me, you will immediately take
it back out and put the
belt on. If you are not me, you will put the belt on
first!! I'm getting pretty good at removing it, by now.
Put the belt on before you put on the thrust bearing...
When you have the spindle in, through the bull gear, step pulley, and
thrust bearing, replace
the thrust collar on the back end, (the small end of the spindle), then
the main spindle gear
and its' key, then screw on the lock collar.
Atlas says to run the collar up to the face of the spindle gear, then
tighten it the space of 1-2
teeth of the gear, rotating the spindle as you do so. They say it
should have some resistance,
so when the spindle warms up it will not have any end play.
Tighten the lock screw on the collar,
(make sure that the thread protecting BB is still in the hole).
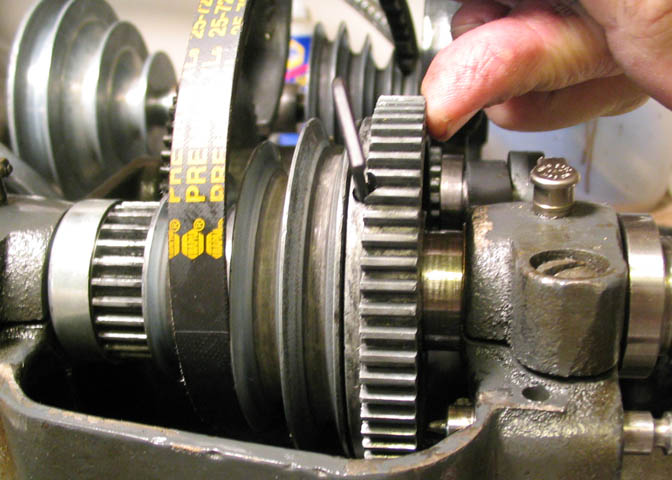
Last step is to tighten the bull gear lock screw. Put the bull
gear right up against the step pulley,
but not riding hard against it. The bull gear and the step pulley
have to be able to turn independently
without rubbing against each other.
Tighten down the bearing caps nice and snug, but don't put all your
might into it. Check to see that
the spindle still turns after tightening them.
To determine how tight to get mine, I put a chuck on the spindle with a
piece of 1 1/2" round stock
sticking out about 2". Then put a DI on the back side of the
round stock, and pulled the stock
toward the front of the lathe and then toward the back of it and
watched the readings. I tightened down
the bearing caps until I had what I wanted, which, for now, was about
one thou at one inch from the chuck
face. How much you cinch down the caps is up to you, but I would
say if you had to use all the strength
in one had on a screwdriver to get what you want, it may be too
much. The bearings caps are a pretty sturdy
part of the casting, but they will only take so much! I will say
now, that this is just a guess derived from
prior practical mechanical experience. I'm no engineer. I
couldn't find any solid info in the Atlas material I
can find, and Clausing didn't have a firm number for me as to torque
when I called them for parts.
Thanks for looking in.
Back to the Atlas Pages
More Taig Lathe & Mill Projects
deansphotographica.com
(home page)
Copyright Dean Williams