A Head Stock Dead Center
for the Taig Spindle Taper
Usually when I turn between centers on the Taig lathe I just put a
piece of stock
in the three jaw chuck and turn a taper on it to use as the head stock
center. Using
the chuck to hold the center allows the chuck jaws to be used to drive
the work piece
dog. However, this limits the distance between centers on an
already small working
envelope. The chuck body and jaws take up room on the spindle
end. Using the Taig
face plate would provide more room, but then there's not a way to hold
a dead center
in the spindle since the face plate covers up the threads on the nose,
meaning you
can't hold the dead center by means of a collet.
There is a simple solution. A dead center made to mount in the
spindle nose taper
with a draw bar to keep it firmly in place does the trick.
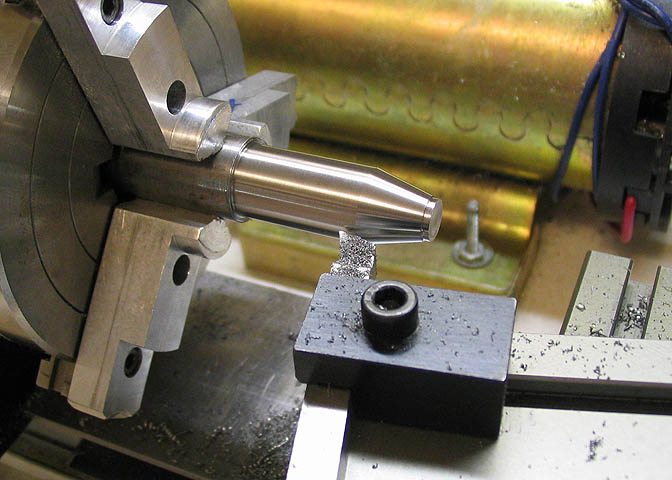
A piece of stock is put in the three jaw and turned down to .530" for a
length of 1.5". Then the
compound is adjusted to 15 degrees and the taper is cut. The
length of the taper can be judged
by holding a stock Taig collet up against the work piece with the end
of the collet facing the
head stock in the same orientation as it would normally be installed in
the spindle. CRS is used.
A small straight portion is turned on the very end of the work
piece. The diameter isn't important
as long as it will fit into the spindle bore. It only needs to be
about .035" long. (It can probably
be left off altogether, but I made it to look like a stock Taig collet.)
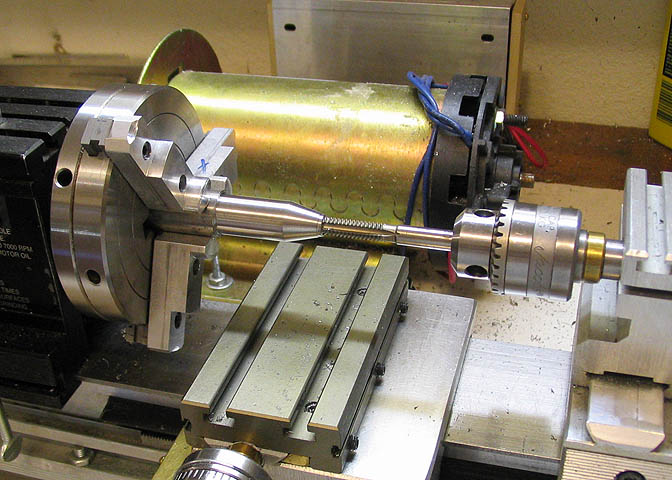
Once the taper is turned, a #7 hole is drilled in the center of the
shaft just to where it would
end at about the front shoulder of the taper. Then the hole is
tapped 1/4-20.
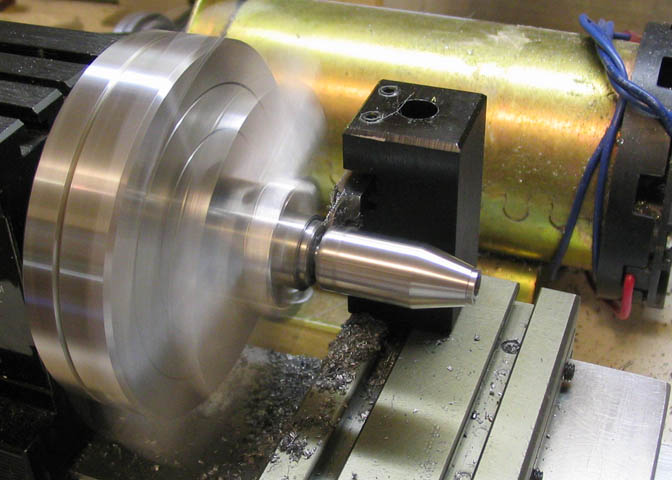
When the work is done on the taper end, it's parted off. About 1
1/2" is long enough.
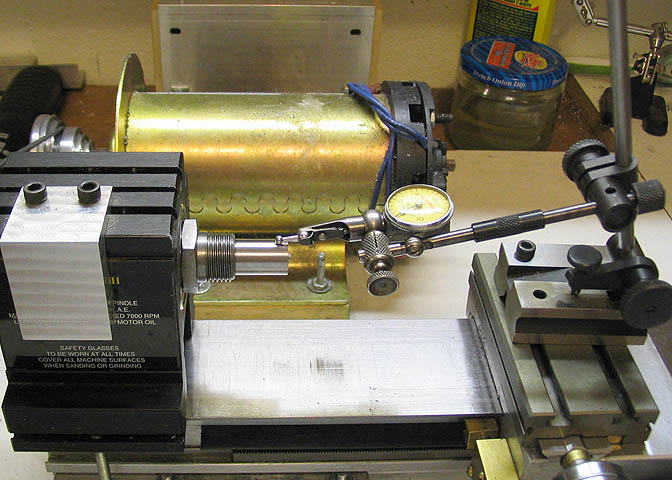
Now the piece can be mounted in the spindle nose taper and cinched down
using a piece of 1/4-20
threaded rod with a washer and nut on the other end. I check the
run out on the piece. Using this old
Starret, it ran out to less than a measurable amount. The
most you can really discern on this type
of indicator is about .0002", so I figure it's less than that, because
the needle doesn't move at all..
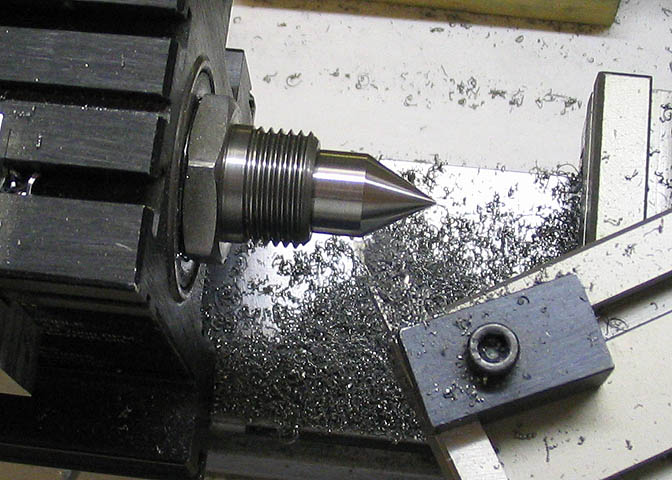
Now a standard center taper is cut on the end of the work piece, and
that's it.
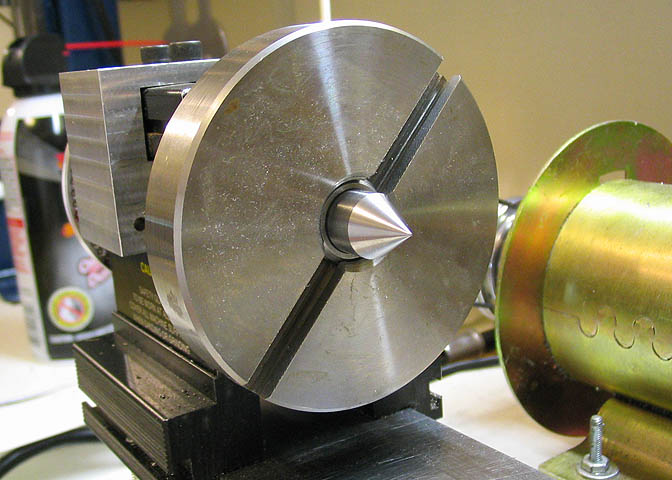
Here you can see that a face plate will mount nicely with the center
protruding enough to make
good use of it. The center can be re-cut many times before it's
too short to use.
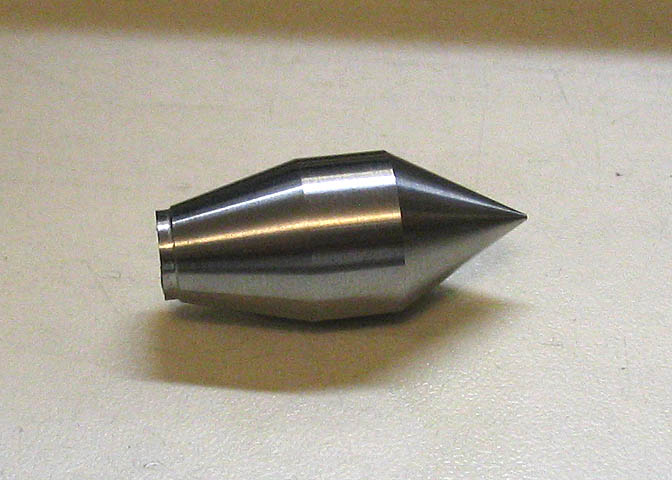
The finished spindle nose dead center.
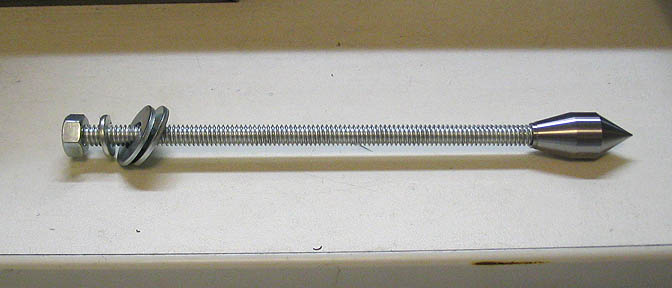
And its' draw bar for pulling it into the spindle taper.
More Taig Lathe & Mill Projects
deansphotographica.com
(home page)
Copyright Dean Williams